The Impact of Technology on Electrical Brass Component Manufacturing
- V Global
- Feb 17
- 3 min read
In recent years, the manufacturing landscape for electrical brass components has undergone a remarkable transformation, driven by advancements in technology. These innovations not only enhance production efficiency but also significantly reduce costs, paving the way for a more sustainable and competitive industry. Let’s explore how these technological advancements are reshaping the brass manufacturing process.
Automation and Robotics: The New Workforce
One of the most significant shifts in brass component manufacturing is the integration of automation and robotics. Automated systems are now commonplace in factories, managing everything from casting to machining. This shift has led to a substantial increase in production speed and consistency. For instance, robots can perform repetitive tasks such as assembling and polishing with precision and without fatigue, allowing human workers to focus on more complex and creative aspects of production.
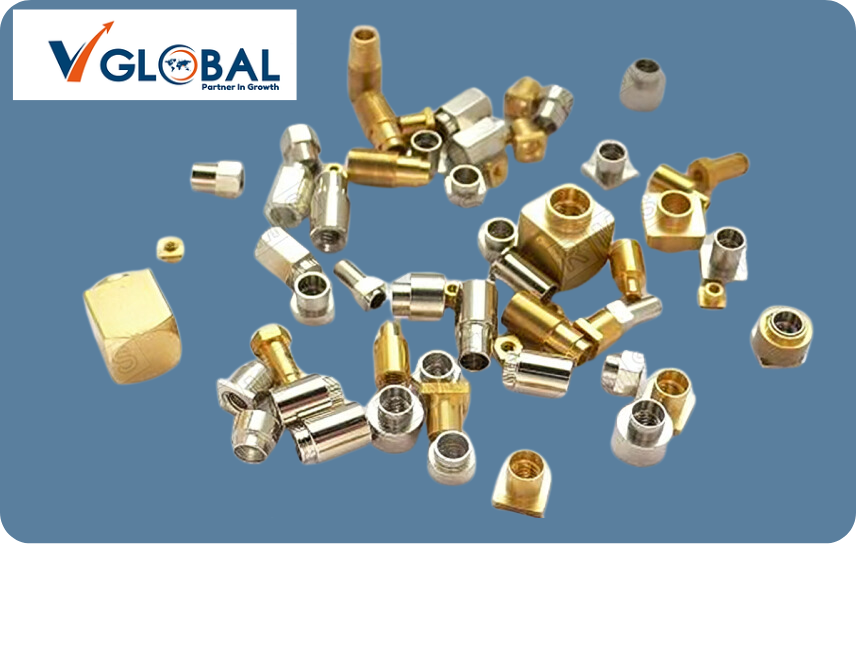
The benefits of automation extend beyond speed; they also enhance safety and reduce human error. By minimizing the reliance on manual labor, manufacturers can achieve higher levels of accuracy while ensuring a safer working environment for their employees.
Precision Manufacturing: 3D Printing and CNC Machining
Precision manufacturing techniques, such as CNC machining and 3D printing, are revolutionizing how brass components are produced. These technologies allow for intricate designs and tight tolerances that were previously unattainable with traditional methods.
CNC Machining: This technology enables manufacturers to create complex shapes with high precision. The ability to customize designs quickly helps meet specific customer requirements without significant lead times.
3D Printing: This method is particularly exciting as it allows for the creation of complex geometries while minimizing waste. By building parts layer by layer, manufacturers can produce unique designs that optimize performance and reduce material costs
Smart Integration: IoT and AI in Manufacturing
The rise of the Internet of Things (IoT) and Artificial Intelligence (AI) is further enhancing the capabilities of brass manufacturing. IoT devices enable real-time monitoring of production processes, providing valuable data that can be analyzed to improve efficiency and predict maintenance needs. This predictive maintenance reduces downtime by addressing potential issues before they escalate into costly failures
Moreover, AI algorithms can optimize production schedules, streamline supply chains, and even assist in quality control by identifying defects during the manufacturing process. This level of smart integration not only boosts productivity but also enhances the overall quality of the final products.
Sustainable Practices: A Greener Future
As environmental concerns grow, sustainability has become a central focus in brass manufacturing. Companies are increasingly adopting eco-friendly practices such as using recycled materials and implementing energy-efficient processes. The emphasis on sustainability not only helps reduce the environmental impact but also appeals to consumers who prioritize green products.
Brass itself is a recyclable material, making it an ideal choice for manufacturers looking to minimize waste. By integrating sustainable practices into their operations, companies can reduce their carbon footprint while maintaining profitability.
Conclusion: A Bright Future Ahead
The impact of technology on electrical brass component manufacturing is profound and multifaceted. With advancements in automation, precision manufacturing, smart integration through IoT and AI, and a commitment to sustainability, the industry is poised for continued growth and innovation. These technologies not only enhance efficiency and reduce costs but also prepare manufacturers to meet future demands in an ever-evolving market.
As we look ahead, it’s clear that embracing these technological advancements will be crucial for staying competitive in the brass manufacturing sector. The future is bright for those willing to innovate and adapt to the changing landscape of manufacturing technology.
For your requirements get in touch with the expert V Global
Comments